Our
products
Specialists in mining equipment.
Produtos
Vibrating Grizzly Feeders
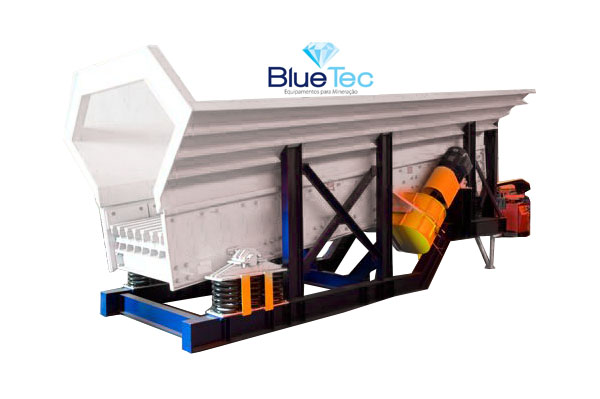
1. DESCRIPTION
Vibratory grizzly feeders are specially designed to accept large feed material used to feed primary and secondary crushers. The structure and vibrators are specially designed to withstand high operating loads and dynamic forces. The vibrating table has adjustable grizzly bars for separation of fine material, combining in a single operation the feeding and pre-classification of the material for the crushers. The grizzly bars can be replaced with a steel plate when no separation is required in the feed material. The vibrating table is fitted with replaceable wear plates and the whole machine is supported on highly resistant helical springs, isolating the machine from the support base.
2. VIBRATING MECHANISM
Our unique patented vibrating system is the heart of BlueTec. The drive structure is compact and incredibly resistant to in order support the tension and compression efforts generated by the vibrators. Each vibrator has two grease lubricating points. Each vibrator uses two selfaligning roller bearings designed for vibrating equipment, and has a double sealing system. Each vibrator is driven independently by an electric motor placed on a stationary pivoted base (non-vibrating).
3. ADVANTAGES:
-Simple maintenance, the “vibrator” drive sets are positioned on the sides of the vibrating feeder, thus being easy to access and maintain.
-Efficiency in separation, its design and its linear movement provide a regular flow of material at a controlled speed, keeping the crusher constant and at full production capacity.
-Structural body free of welds, thus preventing cracks and considerably increasing the useful life of the equipment.
-Adjustment for better productivity, the drive systems are designed to allow adjustments in speed and amplitude of vibration ensuring the best performance for your process.
4. TECHNICAL FEATURES:
We have available two types of feeders, OVF model and suspended OVS model, covering the range capacity from 30 to 500 m ³/ h.
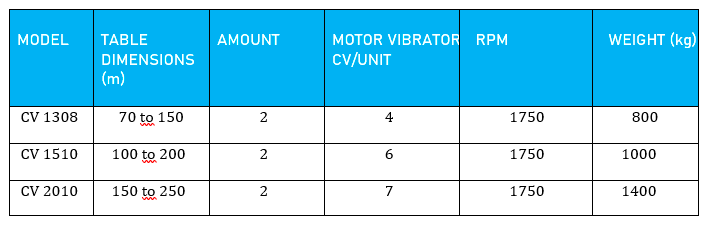
PAN FEEDERS
BlueTec Pan Feeders are used for reclaiming material from a stockpile or hopper in order to ensure a constant feed to other equipment. This equipment is of a simple design, but with a robust construction to withstand the most severe working conditions. It consists of a fixed body attached to the retention unit (tunnel under a silo) which in turn supports the feed through helical springs.
The fixed body has an outlet gate, adjusted by the use of screws, allowing a pre-established volume of material flow. Two vibrators with adjustable counterweights at the ends of their shafts allow a second supply adjustment. The feed chute is lined with replaceable bolted to its structure for replacement when worn out.
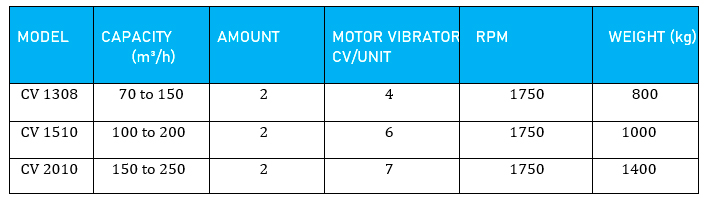
Vibrating Screens
REVOLUTION IN SIEVE TECHNOLOGY
1. Screening Technology
A revolution in screening technology, providing vibrating screens for mineral processing that have the capacity for high tonnage, low operating cost and more capacity than other conventional circular motion screens.
Modular - For maximum operational versatility, inclined, horizontal and multi-angle.
Linear Motion - For rapid separation and high “G” force acceleration.
Structural Strength - For high structural strength long lasting although lighter yet stronger.
Simple Maintenance - For less frequent and shorter maintenance interventions, ensuring maximum availability.
Easy Installation - They can be assembled replacing screens quickly and at low cost.
The patented system of vibrators and linear force vibrating frame provides:
- Linear vibration and a modular design allow you to add and optimize screening variables to ensure the best specific application.
-A greater vibratory force in order to handle high tonnages ensuring better separation
Benefits of the modular screening concept:
- The modules can be placed horizontally, inclined or with multi-angle configurations.
- Each module can be targeted to provide a specific acceleration between 4-8g to maximize screening efficiency and capacity, eliminating blinding and material entrapment, reducing recirculation and minimizing product contamination.
- In wet or dry screening BlueTec offers superior performance.
- Counterweight adjustment from 60% to 100% amplitude, fast and simple, not requiring special tools.
Customize screen decks:
- The decks can be customized in each module, changing the angles, speed and acceleration, for scalping services, classification in dry or wet application.
- The screen mesh can be tensioned laterally or longitudinally, or secured by clamps along the entire surface.
What are the benefits?
- Thinner layer, improving performance.
- Superior screening efficiency, providing cleaner products.
- Increased capacity – more tons of feed per screening station.
- Reduction of the cost of screening with the improvement of the quality of the product.
The Drive System
The vibrator system and its structure with patented support (Brazilian patent granted PI 9914733-5) is the heart of BlueTec.
Many benefits were possible thanks to this linear vibrating force frame QFVL.
The drive structure is compact and incredibly strong, and contains the tensile and compressive stresses generated by the vibrators.
Due to the design of the vibrators it is possible to operate the screen with up to 8g acceleration, if necessary.
Difficult or sticky materials can receive intermittent acceleration of up to 10g when adding a variable frequency control panel.
How it works?
- The vibrators are attached to a linear vibrating force frame QFVL, independent of the structure of the screening module.
This frame supports all the compression and lateral tension generated by the vibrators.
- The side plates are not support for the vibrators, thus eliminating the tensions that in other types of sieves are the main causes of cracks and damage to the side plates.
- The vibrating force frame is mounted at 45 degrees to the horizontal line.
- The vibrators are added by motors in opposite rotation, via cardan shaft. The motors are mounted stationary independently of the screen body, along the sides.
- The vibrators are self-synchronized. There is no interconnection between the vibrators.
- The frame and the force frame are bolted to the side plates with high-strength bolts, forming a highly rigid structure, without the undesirable effects of stress concentration caused by welded connections.
2. Models and Arrangements
BlueTec screens are presented in several models, as single, double, or triple module in adverse inclinations from multiangular to horizontal or even with negative inclination.
It can be from one to four decks. Modules are typically limited to 20 feet (6m) in length and 12 feet (3.6m) in width.
3. Modular System
BlueTec screens can be supported on a “skid” structure made of welded profiles. The modules are designed in such a way that they fit perfectly into the next, allowing material to flow from one module to the next without spillage. The frames have tubular reinforcement in the shape of a diamond for greater transverse rigidity.
4. Linear Vibratory Force Frame
The patented Linear Vibration Force Frame, is made of welded plates, calculated by finite elements in order to guarantee maximum stresses safely. It forms a rigid and independent structure of the screen body. Linear motion action is transferred to the screen body without creating high stresses on the side plates.
5. Vibratory Mechanism
Each module has two grease lubricated vibrators.
Each vibrator uses two self-aligning roller bearings, designed for vibrating equipment, and has a double sealing system.
Each vibrator is driven independently by an electric motor placed on a stationary pivoted base (non-vibrating) where the transmission is made through a cardan shaft.
6. Benefits
- The BlueTec can be equipped with different types of screening media. They can accommodate conventional wire mesh, perforated sheet metal, rubber screens and a variety of polyurethane surfaces.
- Static (non-vibrating) washing system with water sprays over upper deck and between decks is available.
- High efficiency total enclosure system are also available.
What are the mechanical and structural benefits?
- Crack-free structure with long equipment life.
-Easy and low cost maintenance procedures.
-No long, heavy shafts or complex gear boxes.
-Simple amplitude adjustment that can be performed in minutes.
-Lower vibrating mass, which means lower energy consumption and more useful vibration for screening.
BlueTec installation
- New BlueTecs installations use lighter support structures.
- The installation of other screens can be easily upgraded to use a BlueTec screen with increased screening capacity in the same area.
- Modular screens are easier to handle and install than single bodies of conventional screens.
Financial benefits for BlueTec users
- Screen lighter but more resistant, less repair and long structural life.
- Better power-ratio versus tons of feed ensures energy cost reduction.
- Higher “G” accelerations, allow screening of difficult and sticky materials.
- Variables can be adjusted independently to each module for optimized efficiency and production performance.
- Multiple configurations offer maximum screening area in a pre-existing structure.
- Lower installation cost in the modular version than heavy and large single body screens.
- Reduced dynamic loading of the structure, the bracket eliminates harmful vibration and offers quieter operation.
- The drive motors work in pairs and start simultaneously.
- Each vibrator has independent lubrication points. Vibrators as a complete unit can be changed easily and quickly. There are no heavy shafts or large diameter center tubes that require a lot of labor time for disassembly and/or maintenance.
- The vibrators are positioned outside the screen, isolated from dust and water when wet screening, as well as from high temperatures when sieving hot materials.
- BlueTec Screens do not use “V” belts or pulleys.
- BlueTec screens are made up of bolted assembly that facilitates the use and exchange of parts.
- Amplitude change can be done in a matter of minutes, using common tools, and there are 7 adjustment positions.
- Modular design allows material to be rolled or cascaded as it falls from one module to another. This results in better screening quality.
-Elimination of the central tube where the main shaft enters a conventional screen. In this way, access between decks is much easier for maintenance and changing screens.
7. General Specifications
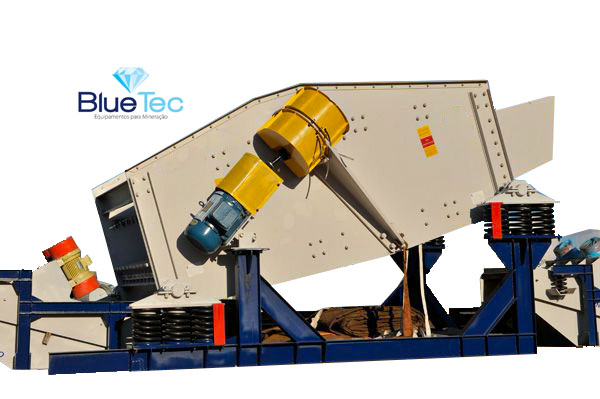
1. Screening Technology
A revolution in screening technology, providing vibrating screens for mineral processing that have the capacity for high tonnage, low operating cost and more capacity than other conventional circular motion screens.
Modular - For maximum operational versatility, inclined, horizontal and multi-angle.
Linear Motion - For rapid separation and high “G” force acceleration.
Structural Strength - For high structural strength long lasting although lighter yet stronger.
Simple Maintenance - For less frequent and shorter maintenance interventions, ensuring maximum availability.
Easy Installation - They can be assembled replacing screens quickly and at low cost.
The patented system of vibrators and linear force vibrating frame provides:
- Linear vibration and a modular design allow you to add and optimize screening variables to ensure the best specific application.
-A greater vibratory force in order to handle high tonnages ensuring better separation
Benefits of the modular screening concept:
- The modules can be placed horizontally, inclined or with multi-angle configurations.
- Each module can be targeted to provide a specific acceleration between 4-8g to maximize screening efficiency and capacity, eliminating blinding and material entrapment, reducing recirculation and minimizing product contamination.
- In wet or dry screening BlueTec offers superior performance.
- Counterweight adjustment from 60% to 100% amplitude, fast and simple, not requiring special tools.
Customize screen decks:
- The decks can be customized in each module, changing the angles, speed and acceleration, for scalping services, classification in dry or wet application.
- The screen mesh can be tensioned laterally or longitudinally, or secured by clamps along the entire surface.
What are the benefits?
- Thinner layer, improving performance.
- Superior screening efficiency, providing cleaner products.
- Increased capacity – more tons of feed per screening station.
- Reduction of the cost of screening with the improvement of the quality of the product.
The Drive System
The vibrator system and its structure with patented support (Brazilian patent granted PI 9914733-5) is the heart of BlueTec.
Many benefits were possible thanks to this linear vibrating force frame QFVL.
The drive structure is compact and incredibly strong, and contains the tensile and compressive stresses generated by the vibrators.
Due to the design of the vibrators it is possible to operate the screen with up to 8g acceleration, if necessary.
Difficult or sticky materials can receive intermittent acceleration of up to 10g when adding a variable frequency control panel.
How it works?
- The vibrators are attached to a linear vibrating force frame QFVL, independent of the structure of the screening module.
This frame supports all the compression and lateral tension generated by the vibrators.
- The side plates are not support for the vibrators, thus eliminating the tensions that in other types of sieves are the main causes of cracks and damage to the side plates.
- The vibrating force frame is mounted at 45 degrees to the horizontal line.
- The vibrators are added by motors in opposite rotation, via cardan shaft. The motors are mounted stationary independently of the screen body, along the sides.
- The vibrators are self-synchronized. There is no interconnection between the vibrators.
- The frame and the force frame are bolted to the side plates with high-strength bolts, forming a highly rigid structure, without the undesirable effects of stress concentration caused by welded connections.
2. Models and Arrangements
BlueTec screens are presented in several models, as single, double, or triple module in adverse inclinations from multiangular to horizontal or even with negative inclination.
It can be from one to four decks. Modules are typically limited to 20 feet (6m) in length and 12 feet (3.6m) in width.
3. Modular System
BlueTec screens can be supported on a “skid” structure made of welded profiles. The modules are designed in such a way that they fit perfectly into the next, allowing material to flow from one module to the next without spillage. The frames have tubular reinforcement in the shape of a diamond for greater transverse rigidity.
4. Linear Vibratory Force Frame
The patented Linear Vibration Force Frame, is made of welded plates, calculated by finite elements in order to guarantee maximum stresses safely. It forms a rigid and independent structure of the screen body. Linear motion action is transferred to the screen body without creating high stresses on the side plates.
5. Vibratory Mechanism
Each module has two grease lubricated vibrators.
Each vibrator uses two self-aligning roller bearings, designed for vibrating equipment, and has a double sealing system.
Each vibrator is driven independently by an electric motor placed on a stationary pivoted base (non-vibrating) where the transmission is made through a cardan shaft.
6. Benefits
- The BlueTec can be equipped with different types of screening media. They can accommodate conventional wire mesh, perforated sheet metal, rubber screens and a variety of polyurethane surfaces.
- Static (non-vibrating) washing system with water sprays over upper deck and between decks is available.
- High efficiency total enclosure system are also available.
What are the mechanical and structural benefits?
- Crack-free structure with long equipment life.
-Easy and low cost maintenance procedures.
-No long, heavy shafts or complex gear boxes.
-Simple amplitude adjustment that can be performed in minutes.
-Lower vibrating mass, which means lower energy consumption and more useful vibration for screening.
BlueTec installation
- New BlueTecs installations use lighter support structures.
- The installation of other screens can be easily upgraded to use a BlueTec screen with increased screening capacity in the same area.
- Modular screens are easier to handle and install than single bodies of conventional screens.
Financial benefits for BlueTec users
- Screen lighter but more resistant, less repair and long structural life.
- Better power-ratio versus tons of feed ensures energy cost reduction.
- Higher “G” accelerations, allow screening of difficult and sticky materials.
- Variables can be adjusted independently to each module for optimized efficiency and production performance.
- Multiple configurations offer maximum screening area in a pre-existing structure.
- Lower installation cost in the modular version than heavy and large single body screens.
- Reduced dynamic loading of the structure, the bracket eliminates harmful vibration and offers quieter operation.
- The drive motors work in pairs and start simultaneously.
- Each vibrator has independent lubrication points. Vibrators as a complete unit can be changed easily and quickly. There are no heavy shafts or large diameter center tubes that require a lot of labor time for disassembly and/or maintenance.
- The vibrators are positioned outside the screen, isolated from dust and water when wet screening, as well as from high temperatures when sieving hot materials.
- BlueTec Screens do not use “V” belts or pulleys.
- BlueTec screens are made up of bolted assembly that facilitates the use and exchange of parts.
- Amplitude change can be done in a matter of minutes, using common tools, and there are 7 adjustment positions.
- Modular design allows material to be rolled or cascaded as it falls from one module to another. This results in better screening quality.
-Elimination of the central tube where the main shaft enters a conventional screen. In this way, access between decks is much easier for maintenance and changing screens.
7. General Specifications
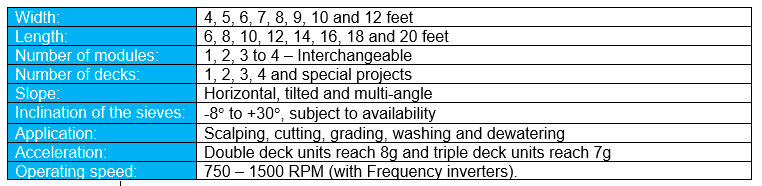
VSI Impact Crusher
DESCRIPTION
BlueTec Vertical Shaft Impact Crushers (VSI) are designed for crushing a wide range of materials such as: stone, ores, minerals, among others. The equipment produces a range of rounded material with “rock on rock” impact technology of fines by varying the rotor speed. The rotor speed can be controlled by use of a frequency inverter on the drive motor.
OPERATION PRINCIPLE
The machine works like a centrifugal pump, and the material is discharged from the rotor at a high speed into the rock lined crushing chamber.
The reduction is obtained by the transfer of kinetic energy that takes place inside the rotor where the material to be crushed is accelerated. The material exits the rotor through the side exit ports. The material at high speed reaches the side wall of the casing and suffers reduction by being at the same time hit by subsequent material, ocurring in this case a chain reaction in the crushing chamber between the wall and the rotor. In this action there is a swirling of material in the crushing chamber, with various modes of reduction such as grinding, impact, shearing, which occurs when the kinetic energy of the material is reduced, which then falls by gravity to the lower discharge.
ADVANTAGES OF VSI BLUETEC
- Produces 100% cubicle product. Which guarantees savings of concrete, asphalt mass and bitumen in asphalt.
- The production of products may vary depending on the rotor speed and the rotor type.
- Can manufacture excellent crushed sand.
- It has a high degree of reduction.
- Hydraulic opening of the top cover allows easy access and quick change of any wear part.
- All work required is done from above.
- It is a proven product with more than 300 machines operating in Brazil.
- Extra efficient rotors with 4 and 5 discharge ports. Up to 40% more efficient than traditional 3 port rotors.
- Extra heavy construction suitable for the most demanding application.
- Fully balanced, allows installation in light structures, not requiring sophisticated foundations.
- Mounted on rubber pads and isolated from the motors, it guarantees its long life.
- Vibration protection prevents bearings damage in case of accidental breakage of the tip.
- When fed properly a limited amount of dust is generated.
TECHNICAL SPECIFICATIONS
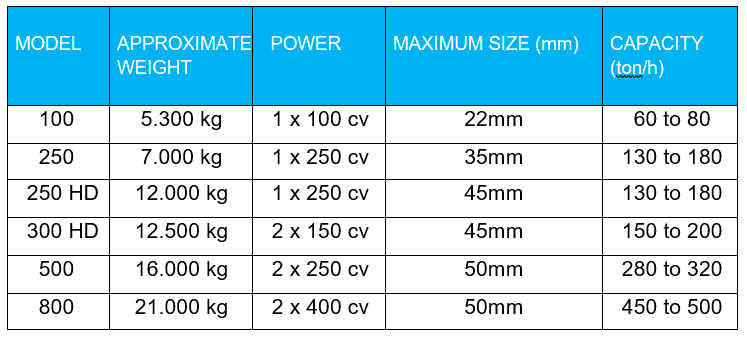
*Capacity table in ton/h measured at the machine inlet, in closed circuit. The capacities shown in this chart are for stone with the appropriate feed size and density of 1.6 ton/m³ and the values are approximate and may vary according to the type (composition) of material to be fed.
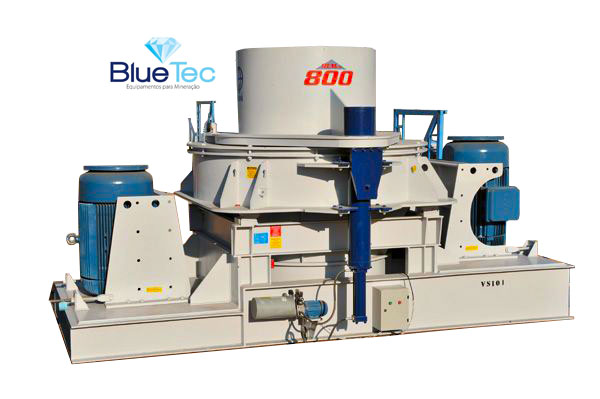
BlueTec Vertical Shaft Impact Crushers (VSI) are designed for crushing a wide range of materials such as: stone, ores, minerals, among others. The equipment produces a range of rounded material with “rock on rock” impact technology of fines by varying the rotor speed. The rotor speed can be controlled by use of a frequency inverter on the drive motor.
OPERATION PRINCIPLE
The machine works like a centrifugal pump, and the material is discharged from the rotor at a high speed into the rock lined crushing chamber.
The reduction is obtained by the transfer of kinetic energy that takes place inside the rotor where the material to be crushed is accelerated. The material exits the rotor through the side exit ports. The material at high speed reaches the side wall of the casing and suffers reduction by being at the same time hit by subsequent material, ocurring in this case a chain reaction in the crushing chamber between the wall and the rotor. In this action there is a swirling of material in the crushing chamber, with various modes of reduction such as grinding, impact, shearing, which occurs when the kinetic energy of the material is reduced, which then falls by gravity to the lower discharge.
ADVANTAGES OF VSI BLUETEC
- Produces 100% cubicle product. Which guarantees savings of concrete, asphalt mass and bitumen in asphalt.
- The production of products may vary depending on the rotor speed and the rotor type.
- Can manufacture excellent crushed sand.
- It has a high degree of reduction.
- Hydraulic opening of the top cover allows easy access and quick change of any wear part.
- All work required is done from above.
- It is a proven product with more than 300 machines operating in Brazil.
- Extra efficient rotors with 4 and 5 discharge ports. Up to 40% more efficient than traditional 3 port rotors.
- Extra heavy construction suitable for the most demanding application.
- Fully balanced, allows installation in light structures, not requiring sophisticated foundations.
- Mounted on rubber pads and isolated from the motors, it guarantees its long life.
- Vibration protection prevents bearings damage in case of accidental breakage of the tip.
- When fed properly a limited amount of dust is generated.
TECHNICAL SPECIFICATIONS
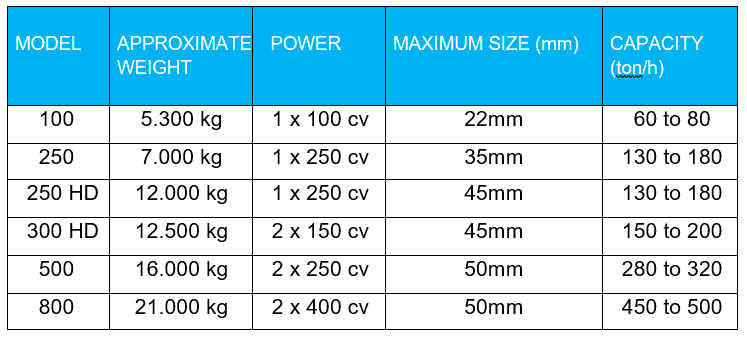
*Capacity table in ton/h measured at the machine inlet, in closed circuit. The capacities shown in this chart are for stone with the appropriate feed size and density of 1.6 ton/m³ and the values are approximate and may vary according to the type (composition) of material to be fed.
HD Cone Crusher
DESCRIPTION
OC HD Series Cone Crushers are robust machines that provide high productivity, low operating cost and long service life, in addition to being the ideal companions for VSI type impact crushers.
Overload safety system uses hydraulic pneumatic pressure accumulators. Due wide opening clearing the machine becomes easy, thus reducing downtime and increasing productivity and reliability.
The adjustment of the Closed Side Setting (CSS) of the machine is through an automatic hydraulic motor, making it possible to make quick adjustments through electric buttons on the control panel.
The crushers are equipped with two hydraulic units, one for lubrication and the other for control. The new composite unit uses advanced technology and is reliable ensuring a longer service life for all components.
An electrical normality of the system adjusts the entire hydraulic lubrication and safety system.
MAIN FEATURES
- Reduction of up to 30% in energy consumption;
- Simple and compact design;
- Large entrance (completely unobstructed);
- Larger feed size capacity;
- High production capacity;
- Easy access to internal components;
- Easy maintenance and low costs;
- Simple and quick control through hydraulic system;
- Low operating cost;
- Ideal for producing feed material for the VSI.
CRUSHING CHAMBER
A new liner technology has been developed for this equipment, where there are slots in the mantle and liner for all available crushing cavities.
This profile allows for better grip of the material to be crushed, also the feed opening allows for the highest feed opening on the market.
In addition to the advantages described, this type of lining profile also allows for greater production capacity, as there is a significant reduction in crushing efforts. In this way, the installed power will be consumed with the increase in production.
TECHNICAL SPECIFICATIONS
PRODUCT GRANULOMETRY TABLE (% throughput in square mesh as a function of adjustment – mm)
PRODUCTION CAPACITY (ton/h) OPEN CIRCUIT
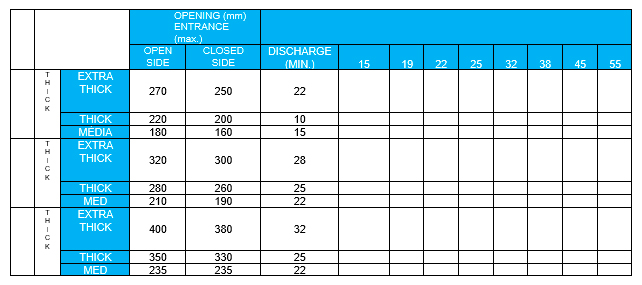
NOTE: Apparent density considered 1.6ton/m³. The established capacity is a help tool for the application of the equipment. However, it is important to consult the factory for the correct application. The real production depends on physical characteristics and proper analysis of the feed material.
NOTE: The dimensions specified above are for information only. For layout studies, contact BlueTec.
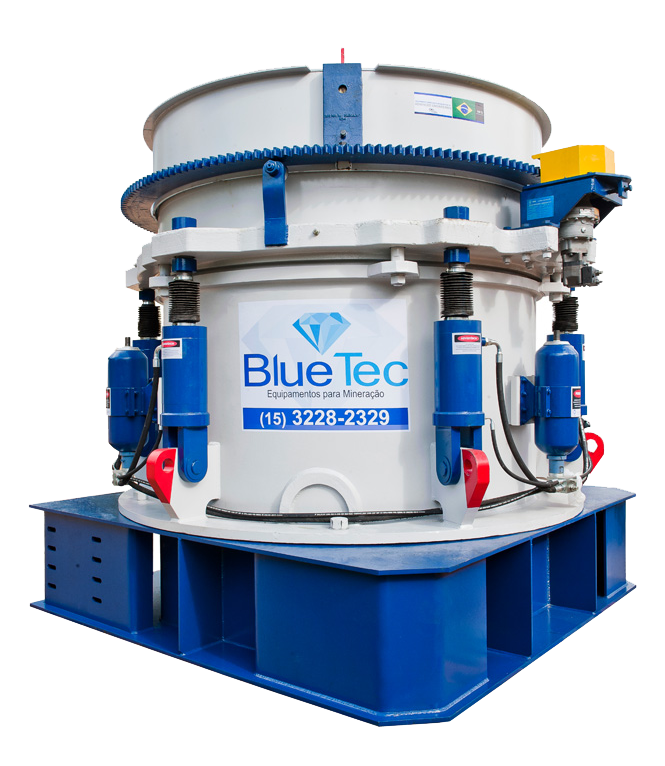
OC HD Series Cone Crushers are robust machines that provide high productivity, low operating cost and long service life, in addition to being the ideal companions for VSI type impact crushers.
Overload safety system uses hydraulic pneumatic pressure accumulators. Due wide opening clearing the machine becomes easy, thus reducing downtime and increasing productivity and reliability.
The adjustment of the Closed Side Setting (CSS) of the machine is through an automatic hydraulic motor, making it possible to make quick adjustments through electric buttons on the control panel.
The crushers are equipped with two hydraulic units, one for lubrication and the other for control. The new composite unit uses advanced technology and is reliable ensuring a longer service life for all components.
An electrical normality of the system adjusts the entire hydraulic lubrication and safety system.
MAIN FEATURES
- Reduction of up to 30% in energy consumption;
- Simple and compact design;
- Large entrance (completely unobstructed);
- Larger feed size capacity;
- High production capacity;
- Easy access to internal components;
- Easy maintenance and low costs;
- Simple and quick control through hydraulic system;
- Low operating cost;
- Ideal for producing feed material for the VSI.
CRUSHING CHAMBER
A new liner technology has been developed for this equipment, where there are slots in the mantle and liner for all available crushing cavities.
This profile allows for better grip of the material to be crushed, also the feed opening allows for the highest feed opening on the market.
In addition to the advantages described, this type of lining profile also allows for greater production capacity, as there is a significant reduction in crushing efforts. In this way, the installed power will be consumed with the increase in production.
TECHNICAL SPECIFICATIONS
PRODUCT GRANULOMETRY TABLE (% throughput in square mesh as a function of adjustment – mm)
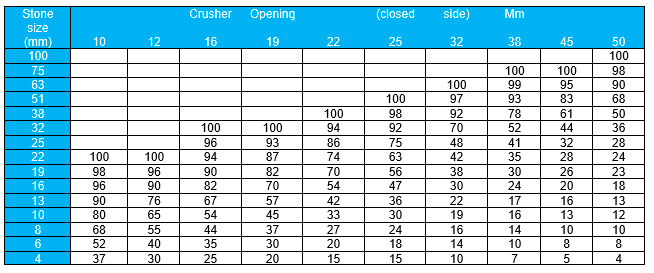
PRODUCTION CAPACITY (ton/h) OPEN CIRCUIT
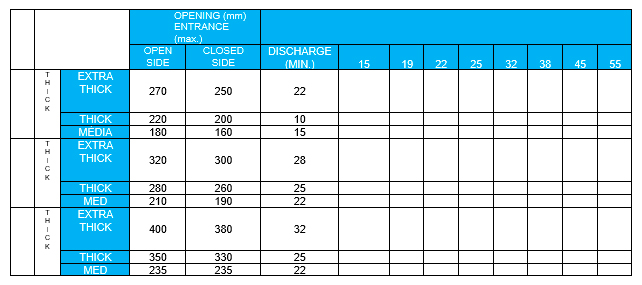
NOTE: Apparent density considered 1.6ton/m³. The established capacity is a help tool for the application of the equipment. However, it is important to consult the factory for the correct application. The real production depends on physical characteristics and proper analysis of the feed material.
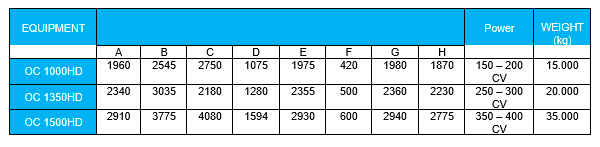
NOTE: The dimensions specified above are for information only. For layout studies, contact BlueTec.
HD Jaw Crusher
DESCRIPTION
BlueTec Jaw crushers are robust machines designed and made with high quality material, aiming at maximum production, reduction of operating and maintenance costs. All wear parts are made from high quality steels. The BlueTec crusher has a reinforced crushing box made of ASTM A 36 steel plate, electrically welded and thermally treated for stress relief, it includes flywheels cast in ASTM A216 steel balanced with high inertia, one of which is machined with grooves for “V” belts, has also the feature of symmetrical chamber thus providing interchangeability for wear parts. The fixed and swing jaw liners are cast in manganese steel and have identical construction, thus making them interchangeable and reversible.
HIGH RELIABILITY
BlueTec jaw crushers feature a heavy-duty design built to withstand the toughest workloads. Castings are manufactured from ASTM A216 steel which, when combined with steel side plates, high manganese jaws and liners, heavyduty eccentric shaft, and four matched super driven bearings, result in superior durability and reliability.
MAIN FEATURES
1 - Symmetric Chamber;
2 - Split Bearing with support bushing;
3 - Fly wheels assembled with Ringfeder;
4 - Extra heavy duty bearings and shaft;
5 - Dry-toggle type shaker;
6 - Unique liners (jaws) (fixed and swing);
7 - Interchangeable side wedges;
8 - Opening adjustments by wedges (automatic);

Capacities are based on granitic rock, cleaned and blasted with apparent density of 1.6ton/m³. Smaller values apply to the feed where material below the APF has been removed. Higher values refer to a feed that includes fines. About 65-85% of the crushed product is less than the APF. The recommended opening depends on the size and crushability of the material fed and the capacity required.
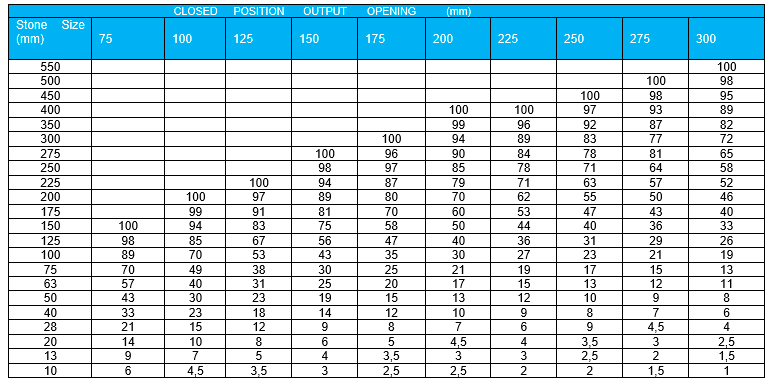


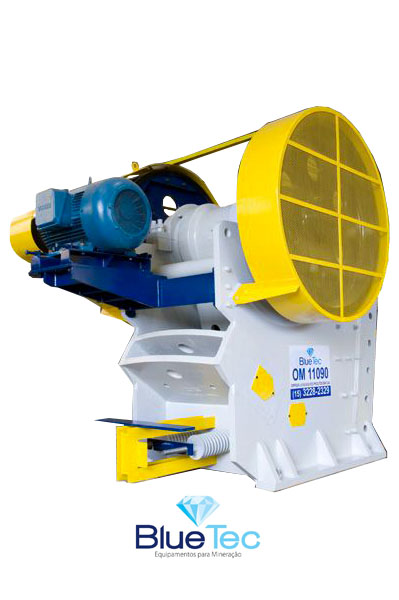
BlueTec Jaw crushers are robust machines designed and made with high quality material, aiming at maximum production, reduction of operating and maintenance costs. All wear parts are made from high quality steels. The BlueTec crusher has a reinforced crushing box made of ASTM A 36 steel plate, electrically welded and thermally treated for stress relief, it includes flywheels cast in ASTM A216 steel balanced with high inertia, one of which is machined with grooves for “V” belts, has also the feature of symmetrical chamber thus providing interchangeability for wear parts. The fixed and swing jaw liners are cast in manganese steel and have identical construction, thus making them interchangeable and reversible.
HIGH RELIABILITY
BlueTec jaw crushers feature a heavy-duty design built to withstand the toughest workloads. Castings are manufactured from ASTM A216 steel which, when combined with steel side plates, high manganese jaws and liners, heavyduty eccentric shaft, and four matched super driven bearings, result in superior durability and reliability.
MAIN FEATURES
1 - Symmetric Chamber;
2 - Split Bearing with support bushing;
3 - Fly wheels assembled with Ringfeder;
4 - Extra heavy duty bearings and shaft;
5 - Dry-toggle type shaker;
6 - Unique liners (jaws) (fixed and swing);
7 - Interchangeable side wedges;
8 - Opening adjustments by wedges (automatic);

Capacities are based on granitic rock, cleaned and blasted with apparent density of 1.6ton/m³. Smaller values apply to the feed where material below the APF has been removed. Higher values refer to a feed that includes fines. About 65-85% of the crushed product is less than the APF. The recommended opening depends on the size and crushability of the material fed and the capacity required.
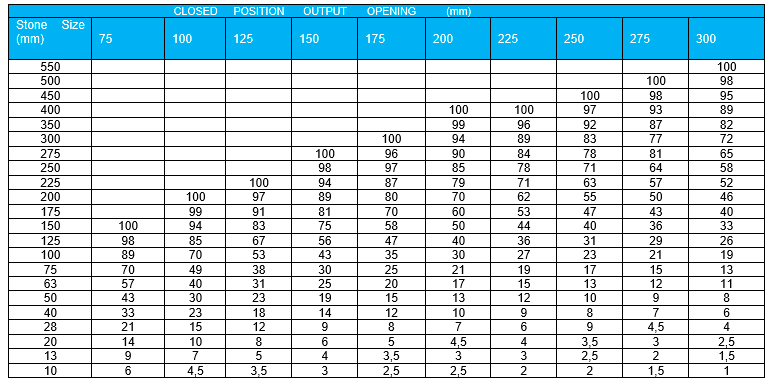


VSI Oil Lubrication System
DESCRIPTION
“Oil Plus” Oil Lubrication system option for Bluetec VSI Bearing Cartridges.
Operational Benefits:
• Higher Shaft rotation speeds, up to 20% higher speeds permitted;
• Reduces daily maintainance, and removes the human error resulting in lack of grease;
• Monitors the condition of the Bearing Cartridge ensuring safe operation;
• The life of the bearings is significantly increased;
• Lower starting torque for easier starting of the machine;
• Totally interchangeable with the standard VSI Cartridge;
• More economical to run than the Standard cartridge;
• Ideal for extreme operating temperatures ensures adequate lubrication in very cold and very hot conditions.
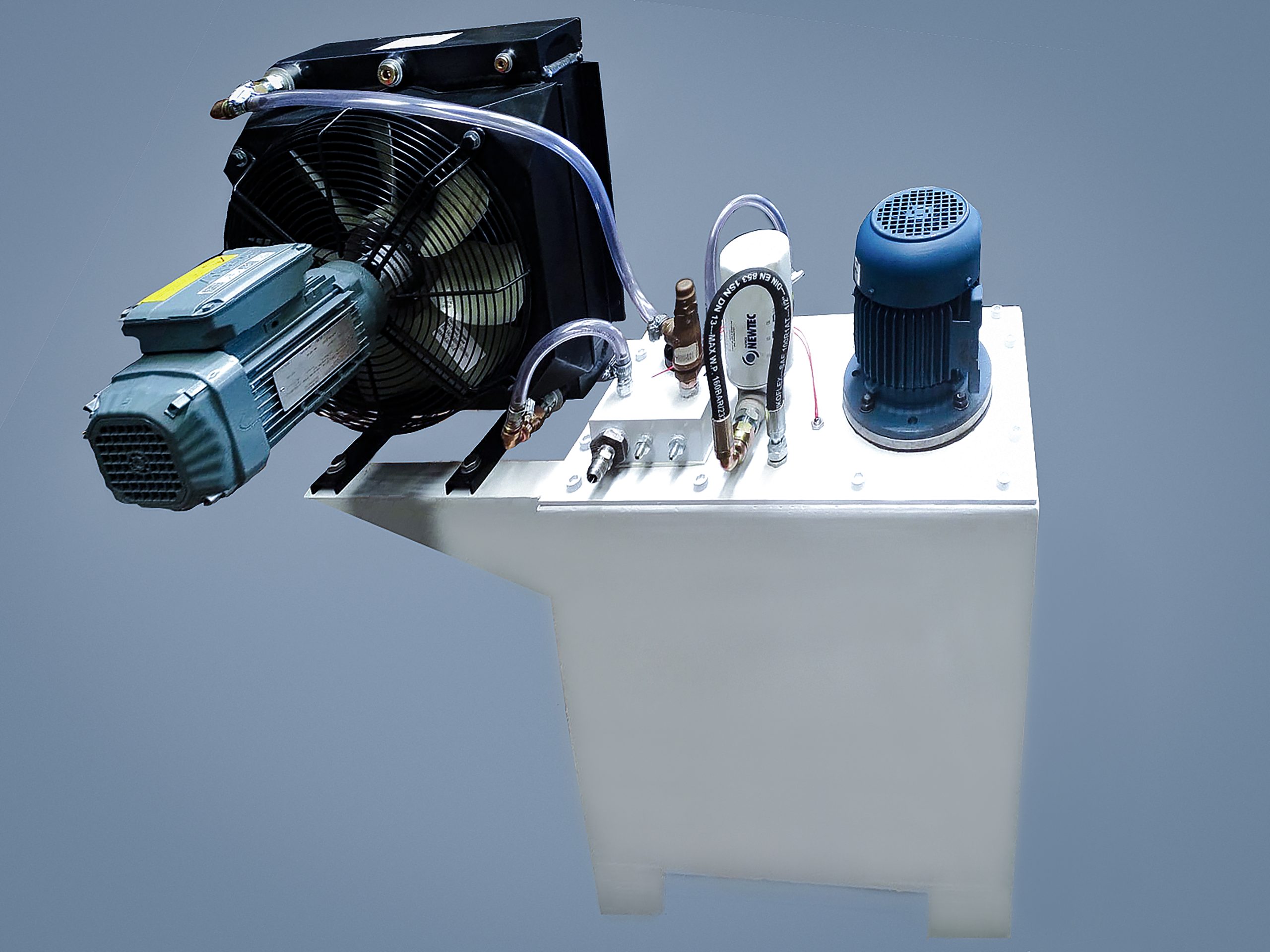
“Oil Plus” Oil Lubrication system option for Bluetec VSI Bearing Cartridges.
Operational Benefits:
• Higher Shaft rotation speeds, up to 20% higher speeds permitted;
• Reduces daily maintainance, and removes the human error resulting in lack of grease;
• Monitors the condition of the Bearing Cartridge ensuring safe operation;
• The life of the bearings is significantly increased;
• Lower starting torque for easier starting of the machine;
• Totally interchangeable with the standard VSI Cartridge;
• More economical to run than the Standard cartridge;
• Ideal for extreme operating temperatures ensures adequate lubrication in very cold and very hot conditions.